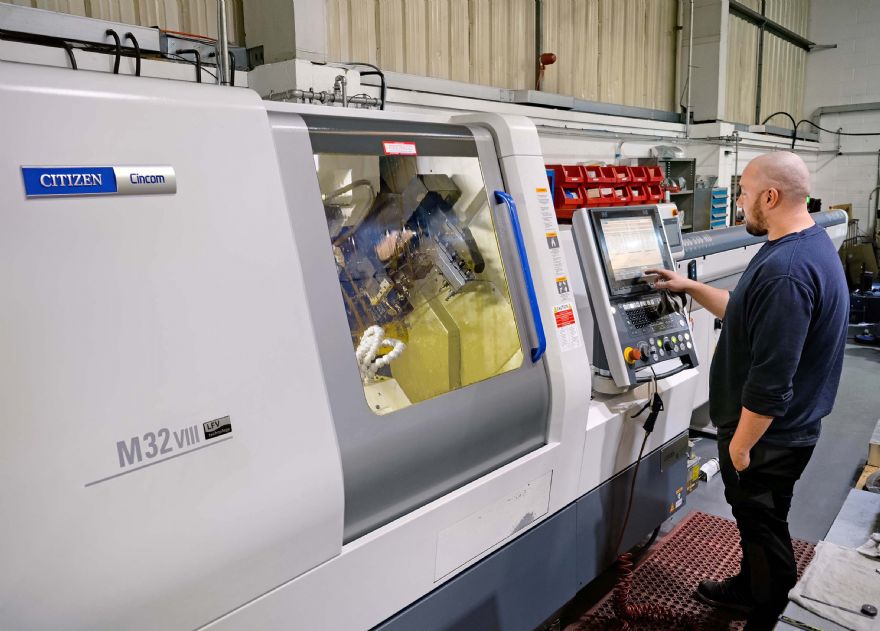
Last autumn (2023), motorsport sub-contractor
h2m needed to replace an ageing sliding-head CNC turn-mill centre in its Hinckley factory. Joint managing directors and owners, father and son team Andy and Martin Forryan, considered buying a replacement from the supplier of the original twin-spindle, 32mm capacity slider, but opted instead for a Cincom M32-VIIILFV supplied by Bushey-based
Citizen Machinery UK.
3,000-off is a large run for sliding-head turned parts at h2m, while production of batches of relatively simple components up to 500-off is typical for unattended overnight running. However, trickier jobs are completed during day shifts in batch sizes as low as 10-off, so speed of programming is essential to minimise machine downtime. Otherwise the reduction in productivity would lower profitability.
Andy and Martin paid particular attention to this issue and came to the conclusion that the Cincom lathe with Citizen’s Alkart Wizard programming system would be less expensive and several times faster than if the other lathe had been purchased. The wizard assists and simplifies the creation of even complex cycles using a built-in code library, reference material and diagrams.
Sharing some detail of their deliberations, Martin said: “Alkart Wizard is an inexpensive option. We use it to prepare programs and prove them out off-line for virtually every sliding-head part we produce. Only the occasional simple component is programmed directly at the control. Even complicated components take just 30 to 40 minutes to program in Alkart and it then takes 15 to 20min to high-speed check the cycle virtually in the wizard, so a new job is always up and running in under 1hr.”
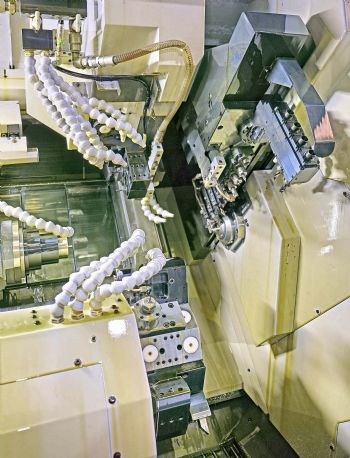
He contrasted this with the much longer and more expensive route that would have been needed with the other slider, for which a similar wizard was not available. First, it would have been necessary to purchase a sliding-head turning software licence for h2m's seat of EdgeCAM, as well as a post processor for the lathe.
Furthermore, creation of the program would have been longer before it could be downloaded to the control, added to which checking the cycle by hand on the lathe would have been very time-consuming, tying up the machine for several hours if it was a complex part. The alternative would have been to acquire third-party verification software, again entailing extra cost. Even then, program creation and prove-out would have taken considerably longer.
Jack Simms, setter-operator of the M32-VIIILFV added: “Basically, the Alkart Wizard is a CAM system and post processor for the Cincom lathe all in one. It is very quick to use and the next program is always ready as soon as the previous batch has finished. We also like the LFV (low frequency vibration) chip breaking software in the lathe control, which is built into the operating system rather than being macro-based.
“It works at both spindles and is an absolute dream. We use it on most jobs, mainly for G71 roughing cycles which tend to produce stringy swarf, particularly when machining heat-treated stainless steels and titanium. LFV is programmed by G-code to turn on when roughing starts and off again when it finishes and is typically used for one-quarter of a cutting cycle. You always end up with short chips, so there are no ribbons tangled around the tool and part."
Everyone at h2m agrees that the Cincom is a stable, repeatable machine that produces parts to within 10µm total tolerance all day long – and to within 5µm with operator supervision. The machine was supplied with a kit that allows over-size bar up to 35mm diameter to be fed into the machine for sliding-head mill-turning. A further benefit is the ability to remove the guide bush, enabling parts up to 2.5xD to be machined more accurately from less expensive bar, in multiple passes if desired, while reducing remnant length threefold. Neither facility had been used by the time the firm was visited in mid-March 2024, by which time 74 different components had been produced on the M32-VIIILFV.
The machine has rapidly proven to be a key facility on the turning side of the sub-contractor’s business, supplementing CNC milling, much of it automated, as well as both die-sink and wire-cut electric discharge machining. The latest lathe acquisition is helping to further the sub-contractor’s success, which is already evident from its current headcount of 49, despite the company having been established by Andy Forryan as recently as 2015. Today, 80% of the firm’s throughput is destined for the motorsport sector, but aerospace work has started to grow and the company is already an established Tier Two supplier.